Color Management from Capture thru Print
A Recent Success Story
Recently we were asked to visit a client regarding consultation for their print production workflows, specifically related to on-going process control. They are a worldwide home decor brand that sells direct to consumer. They have over 1,000 designs to choose from, all of which are printed DTG. They have multiple locations that house over 70, 10-ft wide inkjet printers. So, not only do they create their own designs, but they print all their own products, as well. They also have a photography studio to take pictures of their finished products for use on their online store and in print advertising and their own packaging designs.
While I was initially there to talk with them about print production, I got a tour of their HQ in LA and learned more about what they do. I asked pointed questions about whether they had their cameras profiled and their monitors in the design department calibrated. What I realized and was able to show them is there are huge advantages to color management from the very beginning of the process.
Last month, I went back to fulfill the training and implementation they hired us to do-based on my recommendations. We started with the photography team and studio. We taught them how to create very accurate color profiles of their cameras, lenses, lighting, etc scenarios. No electronic device is accurate, they all have biases that need to be defined and accounted for in order to achieve the most accurate capture. Once we had the profiles built and were able to generate detailed reports on exactly how accurate the profiles were, we showed them how to apply these profiles in post-production. In this process, the images are automatically color corrected to match the original subject matter, thus reducing the amount of time they have to spend color correcting images to match the original subject matter.
We then moved on to their monitors. They had a mix of pretty nice BenQ professional graphics displays and Apple iMacs. They had an existing colorimeter and software that we showed them was not sufficient, so they purchase a new instrument and software that we recommended. Using these new tools, we trained them how to create the best possible calibrations and profiles for their displays. Using these same tools, we can then validate the monitors and generate a complete and non-subjective report showing exactly how accurate their displays were. It was no surprise that their BenQ displays were far better than there iMac displays.
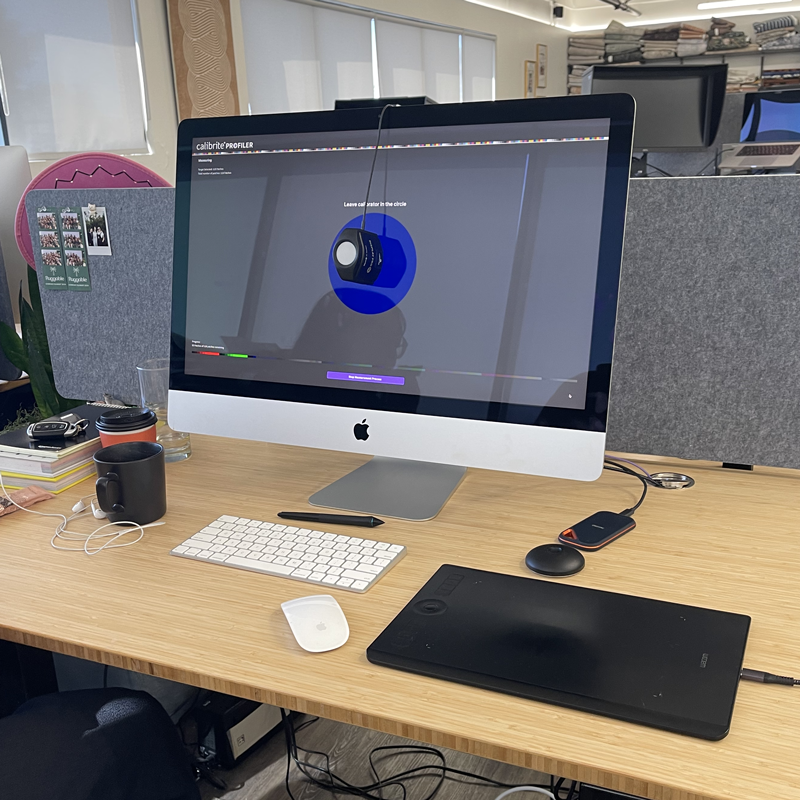
NOTE: The monitor calibration, profiling and validation needs to be done manually. We suggest doing it every quarter, so 4 times per year. This entire process can be automated IF you have supported monitors with built-in measurement instruments (colorimeter). In this case, we have a cloud-based platform where you can schedule all of these functions and “push” them to the displays via the internet. It also provides an online portal where you can see the results of every display, at all locations, and ensure everyone is seeing color accurately in their home or office. I’m also hoping these folks move in this direction but now they’ve got the tools and knowledge to do it themselves, manually.
Now, having a calibrated, profiled and validated monitor is critical for viewing color accurately, it still won’t show how the files will print. When you print the files (let’s say RGB files), they will get converted to a CMYK color space/ICC profile automatically when they get processed thru the RIP/DFE that drives the printers. In order to do this, we taught them how to extract the profiles from print production to use in design for ‘soft-proofing’ on the monitors (among other things, which I’ll get to in a minute). Using Adobe CC applications they can use their print production profiles to now see how their images will look once converted thru the RIP/DFE. This is huge in cutting down cycle times and ensuring their expectations are met.
We spent hours training them exactly how images are captured, where color conversions happen and when, throughout the entire workflow. We taught them the theory of ICC color management, which they cannot get away from because it’s baked into the OS, design apps, as well as RIP/DFE softwares. They had only a basic understanding and said that knowing all this technical stuff was going to help them immensely.
Our training also included detailed discussions about building artwork files properly. Given that many designers these days aren’t totally print-savvy, it’s important to educate them about all of the technical nuances and benefits of building their files correctly. We found several things they were doing that were not ideal and will be collectively formulating new standard operating procedures based on our recommendations.
Lastly, we talked in depth about spot colors. Their products are not actually printed with spot colors but many times they’re trying to match spot colors using their available CMYK gamut. Spot Colors are widely misunderstood. They have a very specific printing process, so we were able to generate spot color libraries, for use in Adobe CC, that were all in-gamut (meaning achievable to match), also using their print production profiles. We also showed them quick and easy to use tools for visualizing and/or determining whether any spot color could be matched (within a given tolerance) and what the ideal CMYK value to use to achieve it.
At the end of the training sessions, they were completely impressed. They now have the knowledge, and they don’t have to wonder about color anymore. They will no longer be chasing color because they know their capabilities and can visualize them way up stream, with ultimate confidence. This minimal investment will pay for itself in a few months time and continue to benefit them for years to come.
Eventually I hope to implement the process control platform I was originally talking to them about. When and if I do, I’ll make sure to write a follow up blog on how that whole endeavor went. Please reach out to us at [email protected] to speak with a color consultant who can answer any of your questions.